Real-Time Vibration Monitoring Using Node-RED and Grafana via OPC UA
- Automate Asia Magazine
- Apr 11
- 5 min read
Updated: 7 days ago

There will always be a level of vibration when machines are in operation, but the intensity of the vibrations may increase significantly over time due to incorrect alignment or imbalance. Pepperl+Fuchs’ vibration sensors reliably detect any changes in these measured values, enabling preventive maintenance before costly damage or failures occur.
From milling machines and pumps to fans and wind turbines, condition monitoring and predictive maintenance play a crucial role in ensuring the safety of personnel and equipment.
In order to perform reliable measurements of vibration velocity and acceleration in low- or high frequency ranges, Pepperl+Fuchs offers three robust vibration sensor series in many environments to prevent untimely breakdowns. The sensors come with analog or IO-Link interfaces, along with global approvals for hazardous areas up to Zone 1/21 and Div. 2, ensuring optimum plant availability and process safety, as well as certifications for functional safety SIL 1/PL c and SIL 2/PL d—meeting the highest safety requirements.
Three Designs for Various Requirements
The vibration sensors by Pepperl+Fuchs feature a particularly large measuring range, capable of measuring vibrations up to 128 mm/s. With encapsulated electronics in a rugged, compact housing, these sensors stand out for their maintenance free operation and long service life.
They are available in three designs with different functional ranges:
VIM3 Series—the Economical All- Rounder
The VIM3 sensors are the smallest vibration sensors in the series, suited for basic and less complex applications. The analog version is optionally approved for SIL 1/PL applications and includes a switching output, which allows direct indication of a critical vibration limit.
Comprehensive Machine Condition Data, Reliable Analysis
The vibration sensor with IO-Link interface, VIM3IO, provides a wide range of measurement values and output data. Values are transmitted cyclically to the controller via the process data, providing in-depth, continuous analysis of the machine’s current condition. This ensures predictive maintenance, enabling plant operators to take appropriate maintenance actions promptly. The wide range of information issued via the sensor includes temperature data, vibration measurements, operating-hours counter, and measurement scaling, enabling data to be interpreted remotely. In addition, the following measured values are transmitted:
Vibration speed (RMS in mm/s) up to 128 mm/s
Vibration acceleration (RMS in g) up to 34 g
Maximum vibration acceleration (peak in g) up to 48 g
Temperature
Crest factor scaled according to DIN ISO 13373-3
Bearing status parameter
Individual Modification via IO-Link Communication
Hardly any machine is the same as another, so the sensors must meet very specific requirements to ensure reliable monitoring. The Pepperl+Fuchs vibration sensor offers customizable parameters that can be modified via IOLink communication. One example is the adjustment of the frequency range to be monitored and the vibration threshold levels related to machine maintenance cycles. Settings can also be input for critical limits for each type of measured value.
Data Storage Function for Simple Commissioning
The numerous customizable parameters of the VIM3*IO* can be optimally adapted to the specific machine properties via IO-Link communication. The settings can be executed either directly in the field or offline, using a desktop configuration.
When customizations are made to the sensor, they are saved as a configuration in the IO-Link master together with a sensor device type ID. If the sensor ever needs to be replaced, the saved configuration is automatically transferred to the new device for quick and easy changeover.
Another feature enabled by the use of IO-Link is that the default setting can be copied from one device to other devices, facilitating quick and efficient commissioning of other devices in the plant.
Frequency Domain Analysis Through BLOB Data Transfer
The sensor can be configured to perform raw data recording. The recorded time domain data can be retrieved by BLOB transfer to the user’s computer for further frequency domain analysis. Frequency domain provides a holistic view of the general health of the monitored machine, facilitating preventive maintenance as abnormalities can be detected early, for example, with the help of artificial intelligence.
Real-Time Vibration Monitoring
As the sensor is often installed at hardt-to- reach locations, the measured values can be retrieved periodically through OPC-UA on Pepperl-Fuchs’ IO-Link masters and stored in on-premises or cloud databases. Users can subsequently create dashboards for data visualization anytime, anywhere. Users may also create push notifications to configured mobile devices so that an alert is sent immediately for any events, for example, when the vibration thresholds are exceeded.
Customized Parameterization Possible from the Factory
As a special service, Pepperl+Fuchs’ sensors can be ordered and delivered with customer-requested settings, once a known configuration is established for a machine type. This can further simplify commissioning, saving time and parameterization setup in the field.
VIM6 Series—Perfect for Extended Temperature Ranges
The sensors of the VIM6 series can measure data for temperature and vibration speed and acceleration. This sensor series is ideal for use in an extended temperature range from –40 °C to 125 °C. They are approved for use in hazardous areas up to Zone 1/21. An analog output is available for each measured value.
Higher-than-normal temperatures may be the result of mechanical wear caused by friction and could result in machine damage. This measured value can therefore provide key information about the machine’s condition. The VIM6 series is available with connector, cable, and duplex steel housing.
VIM8 Series—for Challenging Outdoor Applications
The VIM8 series with encapsulated electronics is designed for use in harsh environments as it withstands notably high mechanical and chemical loads and Zone 1/21 hazardous areas such as mining and offshore applications. The sensors come with SIL 2/PL d approval and a temperature range of –35 … +125 °C. In addition, the vibration sensors are equipped with several sophisticated functions, including integrated vibration evaluation in combination with parameterizable switching outputs. For example, by means of the integrated crest function, the condition of machine bearings can be monitored and machine downtime or failures can be prevented before damage occurs. Optionally, users can define two limit values via rotary switches. As soon as these values are exceeded, they are output via two relays for predictive maintenance purposes. This eliminates the need for extensive software development to evaluate the signal values in a PLC.

Helpful Accessories Complete the Portfolio
The portfolio of vibration sensors is complemented by helpful accessories, including mounting adapters, a flexible metal conduit, and a protective rubber sleeve. The metal conduit, which is available for the sensor types VIM6 and VIM8, safeguard the cables from mechanical stress while the rubber sleeve provides additional protection from moisture and dirt.
Guarantee a Long Service Life, Ensure Efficient Operation
One key area of use
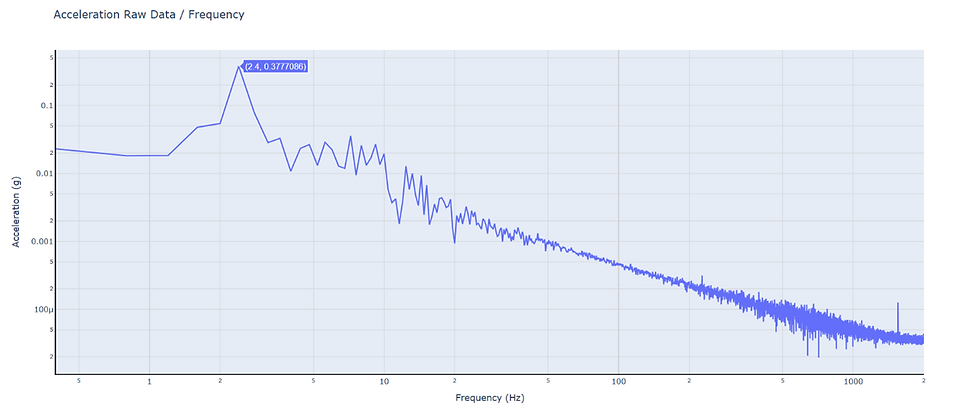
for vibration sensors is pumps and fans, which are required in virtually all industrial sectors. Even in perfect condition, these machines generate vibrations that can be detected by the vibration sensor. Over time, friction or changes in balance will cause wear on the shaft, gear, or other parts. If the vibration levels exceed safe limits, the risk of expensive machine damage and failures increases.
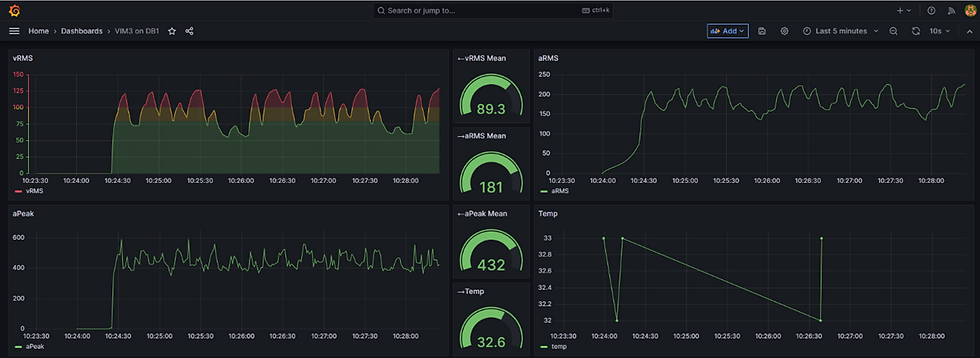
To monitor this, Pepperl+Fuchs’ sensors are mounted on parts such as the bearing unit to monitor the machine condition. Here, the devices provide valuable vibration measurement and analysis data for condition monitoring and predictive maintenance. In this way, downtimes can be kept to a minimum and efficient operation of the plant can be ensured throughout the entire life cycle.