Ifm Condition Monitoring Solution for Pump, A Win-Win-Service for Pentair
- Automate Asia Magazine
- Sep 19, 2023
- 3 min read

A precise look at pump health
At Pentair in Winterswijk, the Netherlands, pumps have been manufactured for over 118 years. The company has grown from a family-owned business into a global leader in water solutions. The pumps and pump systems are designed, produced, and tested entirely in-house. By responding effectively to customers’ needs and developments in the market, the company already has many innovations attached to its name.
Under the Pentair Fairbanks Nijhuis brand, the global company produces smart and sustainable pumping solutions for municipal and industrial water supply. “The pumps are used, for example, in drinking water supply, water treatment, firefighting, regional heating water distribution, and in the onshore and offshore industry,” says Jeroen Munnik, head of the Pentair Service Centre in Zevenbergen, which – together with the Service Centres in Beverwijk and Tynaarlo – ensures that customers receive all the support they need when dealing with pumps: from inspections, preventive and corrective maintenance, the procurement and replacement of pumps to prompt support in the event of acute maintenance needs. In case of emergency, the experts are ready around the clock.
Condition monitoring complements on-site service
For the past three years, Pentair has no longer relied solely on manual service by on-site specialists for customer support. “With our condition monitoring solution Pentair CMD19, we also offer our customers the modern possibilities of efficient demand-oriented maintenance based on the evaluation of the vibration behavior of the system. This can be a pump and an impeller or an industrial fan,” says Jeroen Munnik.
Jeroen Munnik is also convinced by the clear presentation of the vibration values in IFM’s software: “It doesn’t get any better than this, “says Munnik.
Pentair CMD19 was developed together with the automation solutions provider ifm. “At the beginning of our development, we looked around the market and identified ifm as the supplier that completely convinced us in terms of their portfolio, technical support, and assistance.” And so, the complete condition monitoring package includes sensors, diagnostic electronics, and software for vibration monitoring, as well as additional temperature sensors.
“The fact that we have been able to considerably expand our expertise in vibration analysis in the past three years is due on the one hand to ifm’s support, but also to the detailed presentation of the
values in ifm‘s software. Once configured, the traffic light system provides a transparent view of the current health status of the monitored system. It doesn’t get any better than this,” says Jeroen
Munnik.
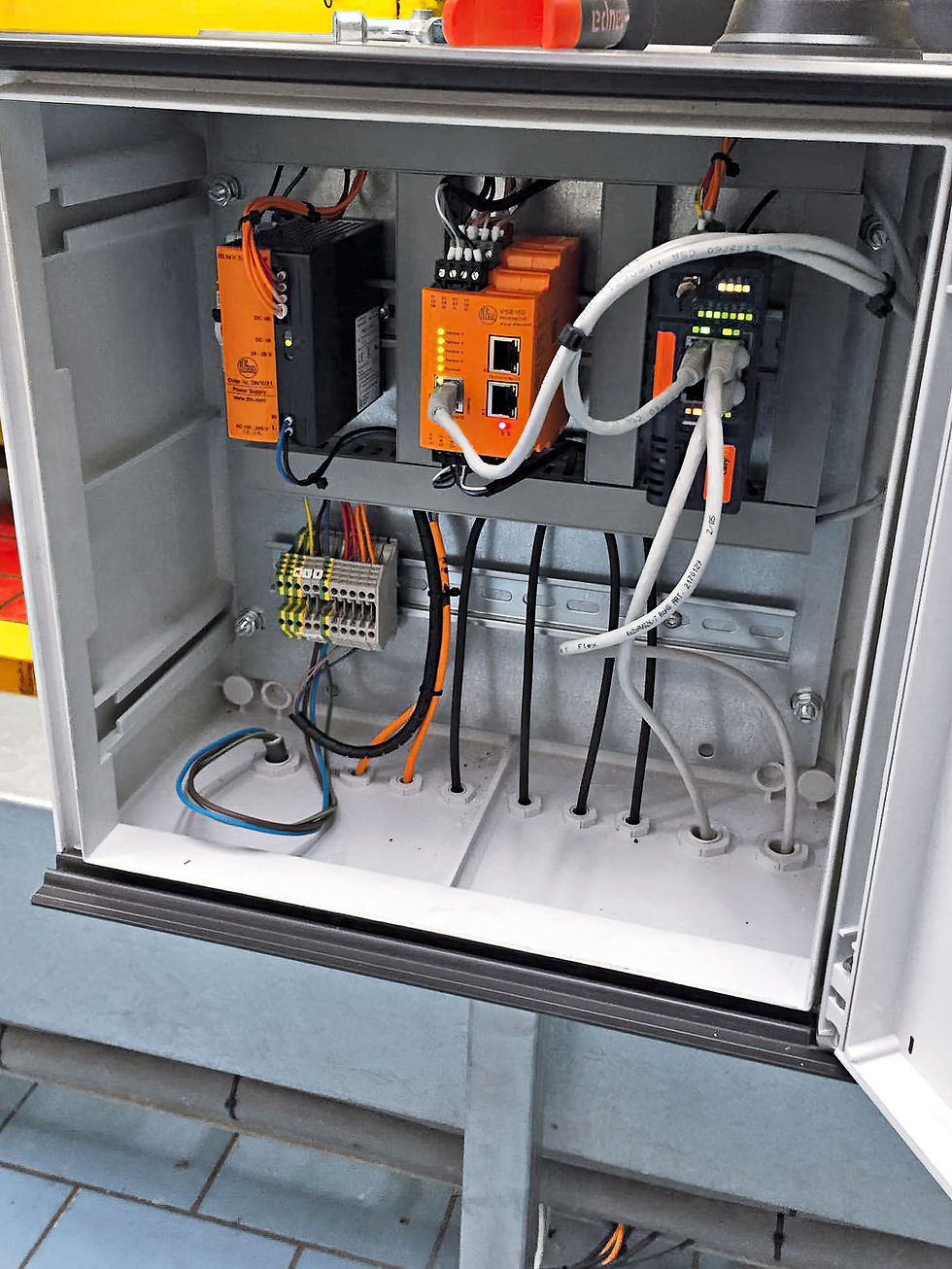
Early detection of maintenance requirements saves money
Customers are also convinced of the automated condition monitoring using sensors. “I remember an incident at a customers’ who installed the modem variant of our solution, the CMD19-M. Through the modem, we directly receive the actual data of the customer’s system. One day we received an alarm and found foreign matter in the pump’s impeller. We informed the maintenance manager, and he was amazed because he had not noticed any change himself. After maintenance and the confirmed findings, he was thrilled that we had saved the company from a more costly repair with possible pump parts replacement.”
This customer saved around 40,000 euros because condition monitoring helped prevent damage to the mechanical seals. Thanks to the expertise gained in vibration analysis, Jeroen Munnik’s team can also forecast error patterns occurring at short notice and take the necessary maintenance measures.
The bottom line is that condition monitoring is an investment in the future that pays off very quickly.
“If we detect foreign matter in the impeller, we can assess whether the blockage will clear up on its own or if the pump needs to be shut down and serviced.”

Investment in the future pays off quickly
Thanks to all these benefits, Munnik sees the future of pump monitoring in condition monitoring. “Whether it is operated on-site by the customer, or whether we act remotely as a service provider, the solution is win-win. The customer and our service team can act in time before significant damage to a pump occurs. At the same time, maintenance staff can be deployed where there is a real need. The early alarm and the condition-based replacement of worn parts ultimately lead to low operational costs. Furthermore, vibration behavior helps us determine the degree of wear and assess whether a component needs replacement at the scheduled time or if it is still functional. The bottom line is that condition monitoring is an investment in the future that pays off very quickly.”
Conclusion
With the help of ifm’s solution portfolio for condition monitoring, Pentair has developed a solution for its customers that maximizes the maintenance effort’s efficiency for both sides. Thanks to the acquired expertise in vibration analysis, Pentair’s Dutch team can support its customers with precise fault assessments and recommendations for action to lower the total cost of ownership.