The past few years have shown just how vulnerable the global supply chain is to disruptions. The COVID-19 pandemic brought unprecedented challenges for manufacturers everywhere and the cross-border flow of materials and components. With added climate change challenges and an ever-evolving geopolitical landscape, such disruptions seem to be more frequent and intense. To thrive in this dynamic environment of constant change, manufacturers can leverage digital technologies to find new ways to protect their supply chains amid uncertainty.
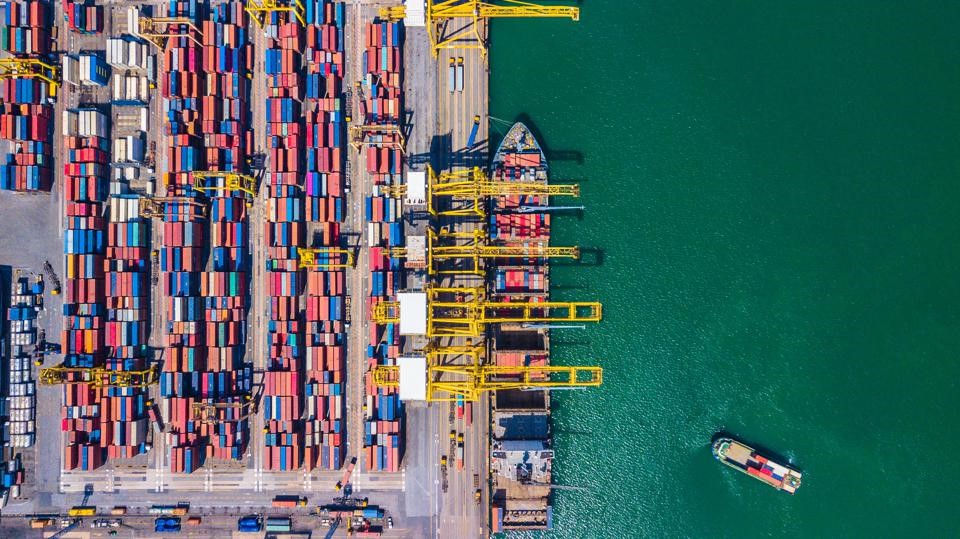
One strategy companies are employing is known as “nearshoring”, which involves locating or investing in manufacturing capacity closer to the end customer, target market or corporate hub. To maximize the logistical and operational benefits, nearshoring must be about more than just where factories are located, but also how their manufacturing operations are evolving. To that end, Industry 4.0 applications, technologies and processes — and the connectivity that enables them — are essential to maximizing agility, planning capacity and output.
The push and pull to closer shores
Companies have long placed manufacturing facilities “offshore” to take advantage of lower production costs, and readily available labor. However, as they became single modalities, this operating model proved under pressure to become a logistical liability.
More and more, manufacturers are turning to nearshoring to insulate their supply chains from future disruption. In fact, 70% of U.S. manufacturing companies plan to establish or relocate production capacity closer to home, their customers, or potential buyers, according to a recent survey by ABB’s robotics and automation division.
Nearshored production offers more than supply chain resilience. Being close to customers leads to faster response times and eases adjustment to evolving regional requirements and regulations. Shipping is quicker and less expensive, and time-to-market falls. Localized factories can do away with customs and duty charges to customers, and reduce the impact of currency fluctuations.
But the most dramatic operational and productivity benefits will come to those companies that equip their nearshored facilities with Industry 4.0 technology and applications.
Stepping into the Industry 4.0 facility
In an Industry 4.0-enabled facility, advanced robotics can move products to, from and around production, warehouse and loading areas, streamlining operations while protecting employees from potentially dangerous work. Sensors throughout the plant collect data that’s analyzed by cyber-physical systems and artificial intelligence, improving agility and real-time optimization of operations and workflow processes. Augmented reality and virtual twinning can create detailed digital representations of products, eliminating the need to reconfigure factories to manufacture prototypes and test models. Highly automated and flexible operations equipped with human augmentation will also help companies struggling with the availability of skilled labor in some markets and will give rise to a “new collar worker” according to Bell Labs Consulting.
It's an enticing picture. But making it real requires the right networks and connectivity. That means a robust, on-premises wireless network to connect to machines and workers, and an agile edge cloud infrastructure to connect the wireless network to applications running on local servers.
Flexibility on the factory floor
A factory is not a static environment. Product lines often need to be reconfigured or adjusted to respond to market needs. Factories also tend to have challenging layouts filled with obstructions, which can make it difficult to hardwire devices to a network. A private wireless network (either 4.9G/LTE or 5G) is well-suited for the untethered devices and business-critical applications that operate in these environments. A private wireless network offers the high bandwidth, high reliability and very low response times that are required for many applications. For instance, autonomous mobile robots can seamlessly operate across the factory floor to move product parts and tools, speeding up final assembly. And AI and AR/VR technologies can enhance the day-to-day of workers, from immersive on-the-job training to interactive digital representations of factory environments and machines.
Time-sensitive Industry 4.0 applications, such as augmented reality and process automation, require real-time data processing, making it important to keep them on-premises for the fastest response times. Edge-compute is a reliable solution for such technologies, demanding a robust wireless network on-premises and an equally agile Ethernet network.
Beyond on-premises
Nearshored facilities don’t operate in a vacuum, making high-performance, on-premises wireless just one requirement for the Industry 4.0 facility. Manufacturers and warehouse operators will need ready access to corporate assets living in the private cloud, like design documents and production specifications, and resources for essential activities such as email and enterprise resource planning.
Also critical is an elastic and flexible computing pool spread across data centers and the public cloud, enabling enterprise applications to scale and evolve to support more users and new use cases. Data center networks must be equally agile so they can synchronize with changing applications while delivering the connectivity needed.
Robust connectivity is key
Taking full advantage of nearshoring means thinking network first. The optimal nearshored facility attains maximum agility, adaptability and production capacity through Industry 4.0 technologies and applications, enabled by the reliable, secure and business-critical connectivity of an on-premises private wireless network, the underlying edge network, and a wide area network linking the facility with corporate resources across its cloud infrastructure.
Source: www.forbes.com